The noise reduction of high-temperature melt pumps is achieved through gear improvement?
As a professional high-temperature melt pump production enterprise, the company has decades of experience in the research and development and production of high-temperature melt pumps, providing high-temperature melt conveying and metering equipment with displacement ranging from 1CC to 12000CC, to meet the production needs of different working conditions. This article elaborates on how to design gears to achieve the purpose of reducing noise during the operation of high-temperature melt pumps.
1. Using fine and high teeth
On the basis of ensuring the strength of the gear, adopt a maximum tooth height coefficient as much as possible. This can not only increase the overlap, but also increase the flexibility of the gear teeth due to the thinning of the tooth roots, making it easier to absorb the vibration of the gear teeth. However, it is also necessary to pay attention to the conditions for increasing the tooth height coefficient: a. The tooth top width of the gear cannot be less than 0.3mn; b. There is no interference between the root and top of the teeth of the meshing gear.
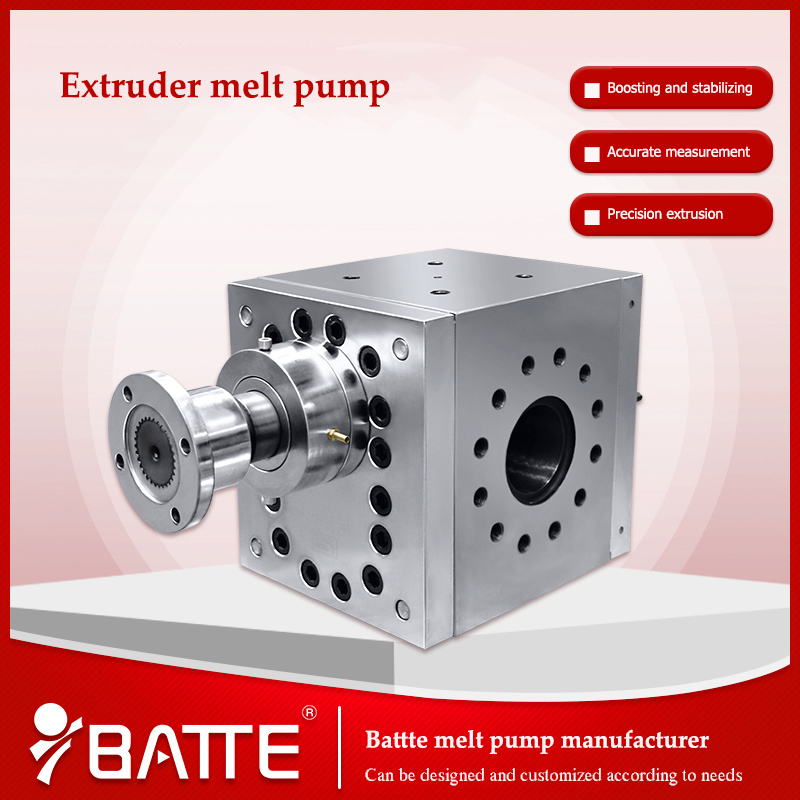
2. Changing the modulus and number of teeth
The rigidity of gears generally increases with the increase of modulus. For gears with larger transmission power, the bending deformation of the tooth root is the main influencing factor, and a larger modulus should be selected. The higher the modulus, the lower the noise. For gears with generally low loads, smaller modules should be selected as much as possible, as machining errors are the main influencing factor at this time. Moreover, a smaller module can increase the number of teeth and increase the overlap, which is beneficial for improving transmission stability and reducing noise. Both modulus and number of teeth have an impact on the natural frequency of the meshing system, and should be comprehensively considered during design.
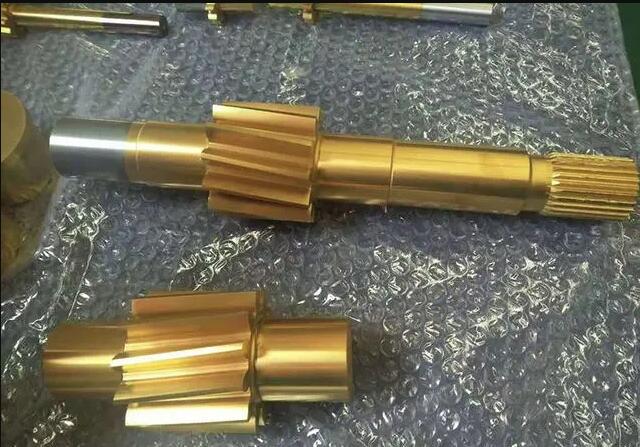
3. Increase overlap and displacement
The greater the overlap, the smoother the gear transmission, which is more conducive to reducing noise. Therefore, helical gear transmission should be preferred. Positive displacement of the driving gear can lengthen the meshing line segment at the top of the gear teeth, while increasing the gear stiffness, which is beneficial for reducing noise. The determination of gear modification coefficient is a very important factor in gear design. It not only affects the strength of gears, but also affects the meshing noise of gears.
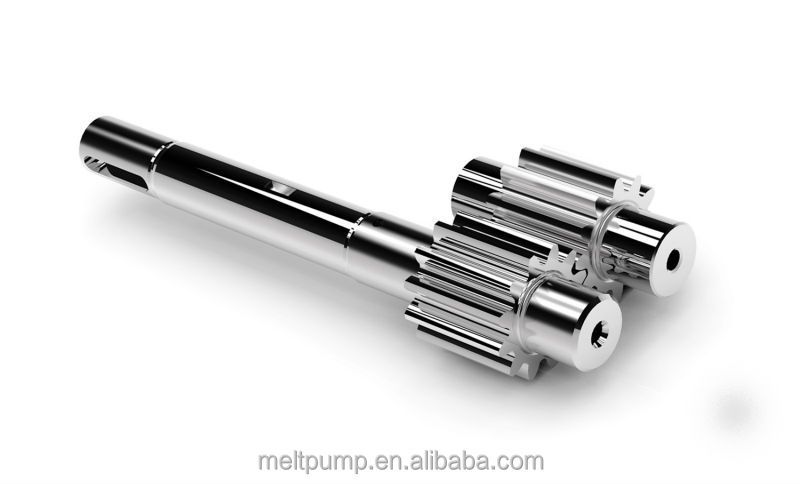
Gears not only achieve the goal of reducing noise through design, but also take measures to reduce noise during the manufacturing process. The commonly used machining process for cylindrical gears is the rolling and grinding process or the rolling and shaving process. The tooth shape accuracy of gears during gear hobbing not only depends on the accuracy of the hob and machine tool, but also has a close relationship with the installation accuracy. If the accuracy of the machine tool and the hob is guaranteed, the installation accuracy of the hob is particularly important. The higher the installation accuracy of the hob, the smaller the tooth profile error value, and the lower the operating noise.
Email: info@battemachinery.com
Whatsapp: +86 158 38331071