Plastic extrusion melt pumps for pipe extrusion lines
Plastic extrusion melt pump plays an important role in pipe extrusion line, its core advantages are reflected in the stabilization of pressure, precise flow control, homogenization of the melt, reduce energy consumption and extend the life of the equipment, etc., as follows:
Pressurization and pressure stabilization: The melt pump receives the high temperature plastic melt from the extruder and pressurizes it to ensure that the melt is delivered to the extruder head at a sufficiently stable pressure. In the production process, even if there are fluctuations in the melt pressure output from the extruder, the melt pump can buffer and eliminate such fluctuations through its own work to ensure that the melt enters the head at a stable pressure, which is crucial to the quality of pipe molding. For example, in the production of some special pipes with high pressure requirements, the pressurizing and stabilizing effect of the melt pump can ensure the wall thickness uniformity and dimensional accuracy of the pipes.
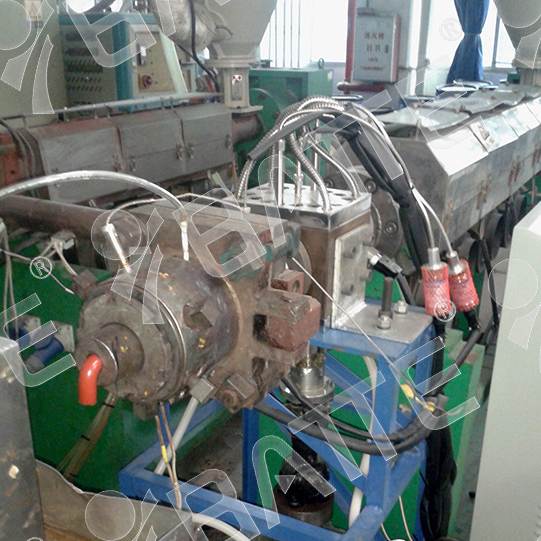
Precise flow control: By adjusting the rotational speed of the melt pump, the melt flow can be precisely controlled. Since the melt pump is a positive displacement conveying device, its flow rate is strictly proportional to the rotational speed, so it can provide the extruder head with an accurate and stable melt flow rate, thus ensuring the stability of the pipe extrusion speed and output.
Homogenizing the melt: During the melt conveying process, the rotation of the gears or screws of the melt pump produces a shearing and mixing effect on the melt, resulting in a more homogeneous composition of the melt and improving the homogeneity and stability of the melt. This helps to reduce stress concentrations within the pipe and improve the physical properties and quality of the pipe. The homogenized melt reduces imperfections on the pipe surface, such as flow marks and bubbles, resulting in a higher surface finish and better appearance.
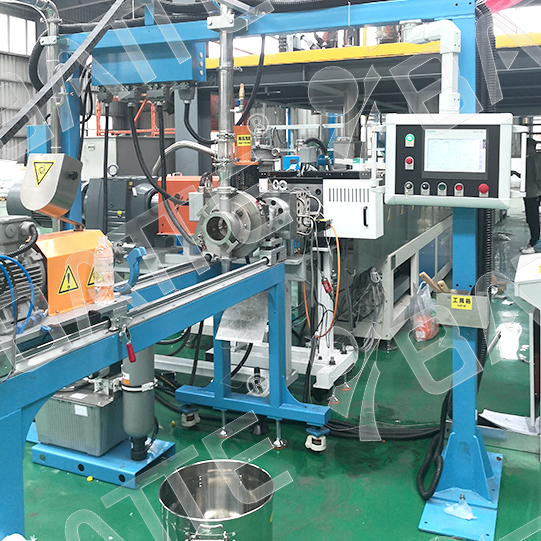
Improve production efficiency: Melt pump can reduce the workload of the extruder, so that the extruder can focus more on the melting and mixing of the material, and improve the working efficiency of the extruder. Stable melt supply and precise flow control help the production line to enter into a stable working condition quickly, reducing the debugging time and the number of stoppages in the production process, thus improving the overall production efficiency.
Reduced energy consumption: The melt pump can transfer the depressurization function of the extruder to itself to complete, so that the extruder can work in a low-pressure and low-temperature state, the leakage flow is greatly reduced, thus reducing the energy consumption of the extruder. Accurate flow control can avoid the waste of energy caused by too much or too little melt flow, and improve the efficiency of energy utilization.
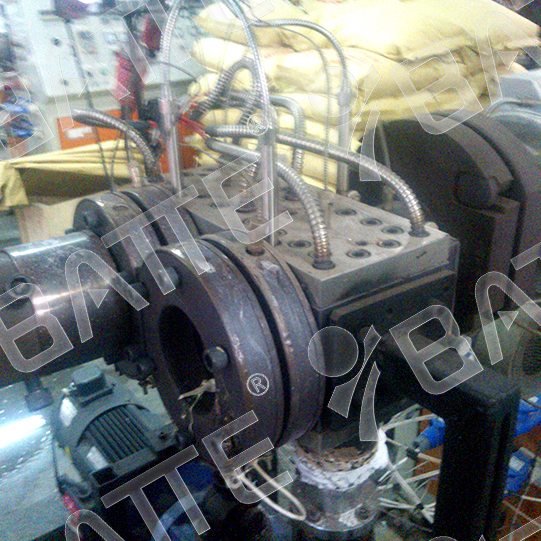
Extend the life of equipment: after using melt pump, the pressure inside the extruder decreases, the wear between screw and barrel is reduced, and the load on the thrust bearing of the gear box is also reduced, thus extending the life of the extruder and related equipment. Stable operation of melt pumps can reduce damage to equipment caused by pressure fluctuations and overloading, etc., and reduce equipment maintenance costs and repair frequency.
Email: sale@meltpump.com
WhatsApp: +86 158 38331071