chemical melt gear pump for twin screw extruder
The combination of co-rotating twin-screw and high-temperature melt pump technology realizes a new one-step process of polymer compounding and direct extrusion, which can significantly reduce costs, save energy and reduce the performance of polymer materials due to repeated heating. Typical applications are PE, PP biodegradable sheet molding and extrusion, direct blending and blow molding of PE functional films, etc.
The main function of the melt pump is to pressurize and stabilize the high temperature plastic melt from the extruder and then send the flow rate to the extruder head in a stable manner. Its ability to stabilize melt pressure and flow rate is better than various types of extruders. When it is used in tandem with single-screw or co-rotating twin-screw extruders, the efficiency of the whole production line can be increased significantly. The necessity of applying melt pump is.
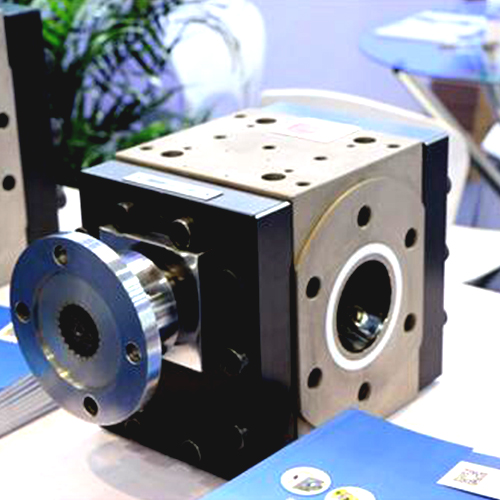
1、High precision: It can achieve stable extrusion, improve the dimensional accuracy of extruded products and reduce the scrap rate. In the extrusion process, it is difficult to avoid the uneven amount of material feeding, the fluctuation of barrel and head temperature, and the pulsation of screw speed. The use of melt pump can eliminate the charging error of the charging system, which can greatly reduce the fluctuation of the upstream process transmission and quickly enter the stable working condition, improve the dimensional accuracy of the extruded products and reduce the scrap rate.
2, low energy consumption: the combination of co-rotating twin-screw extruder and melt pump into a mixing extrusion pelletizing production line, its mixing quality and output than a separate twin-screw pelletizing set significantly improved. The energy consumption of processing each kilogram of material can generally be reduced by about 25%.
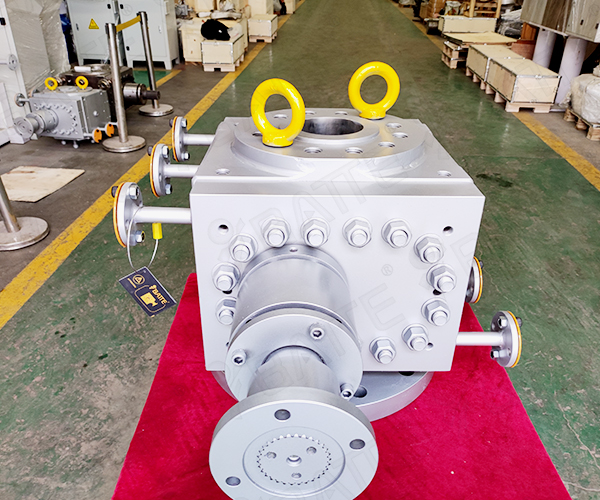
3, save process: in the original is a single screw or the same direction twin-screw pelletizing extruder to add melt pump and pipe, plate, film and other extrusion head, you can omit the pelletizing process directly extruded products. This system is ideal for extruding products with materials that need to be co-mingled and modified. In addition to the advantages of No. 2 above, this system also achieves energy saving by simplifying the production process of extruded products and shortening the production cycle.
4、Long life: The use of melt pump reduces the pressure in the extruder barrel, which can greatly reduce the wear between the screw and barrel, reduce the load on the thrust bearing of the gear box, and extend the life of the extruder. The extruder in the production process need to exhaust the material problem can also be solved.
5、Easy to detect: The melt pump has linear extrusion characteristics, which makes it easy for upstream and downstream equipment to work in coordination. As the melt pump leakage flow is less, the pump's conveying capacity and speed are basically linear, the flow rate of the melt pump can be known exactly after the speed change, as the working speed of the upstream and downstream equipment synchronized with the gear pump can be determined, and the whole extrusion process can be monitored online and controlled by feedback using the information data of pressure and temperature collected at the entrance and exit of the melt pump.
Email: info@battemachinery.com
Whatsapp: +86 158 38331071