What are the technical advantages of elastomer extrusion melt pumps?
Rubber extruder melt pumps (rubber melt gear pumps) are the core equipment of rubber and elastomer extrusion systems, and their applications cover the precise conveying and metering of high-viscosity, heat-sensitive materials.
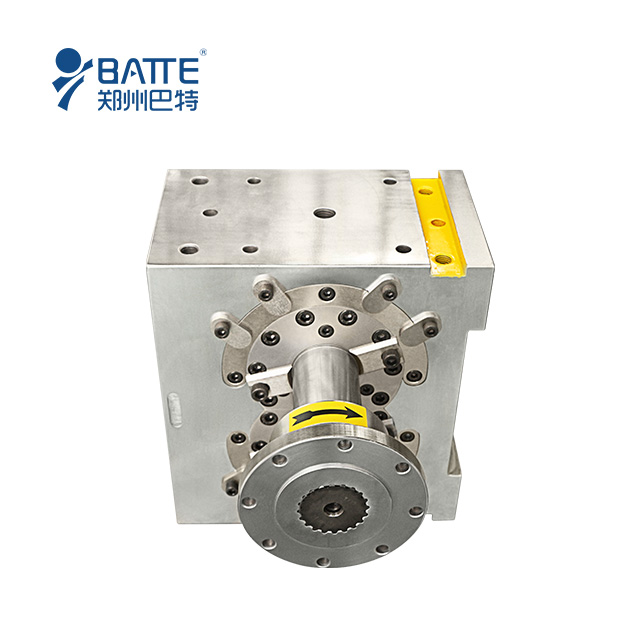
Key Technical Advantages
Pressure and flow stability
Eliminate the effect of extruder screw pulsation on the melt, die head pressure fluctuation ≤ ±1%, significantly reduce product thickness deviation (e.g., hose wall thickness tolerance can be controlled within ±0.05mm).
Self-cleaning and low-residue design
adopts precision-machined rotor-stator mating structure, which generates shear force during rotation to clean the pump chamber automatically, avoiding carbonization or degradation of materials, especially suitable for production scenarios with frequent color or material changes.
High temperature and high pressure adaptability
Working temperature range: ≤350℃ (some models can reach 400℃);
Outlet pressure: ≤40MPa, to meet the needs of high-resistance mold or long process extrusion.
Energy saving and equipment protection
Transfer the function of extruder pressure reduction to melt pump, so that the screw works under low pressure and low temperature (≤300℃), the leakage flow is reduced by more than 30%, and the energy consumption is reduced by 15%-20%;
Reduce the screw axial force, and prolong the life of the equipment (usually can be extended by 1-2 years).
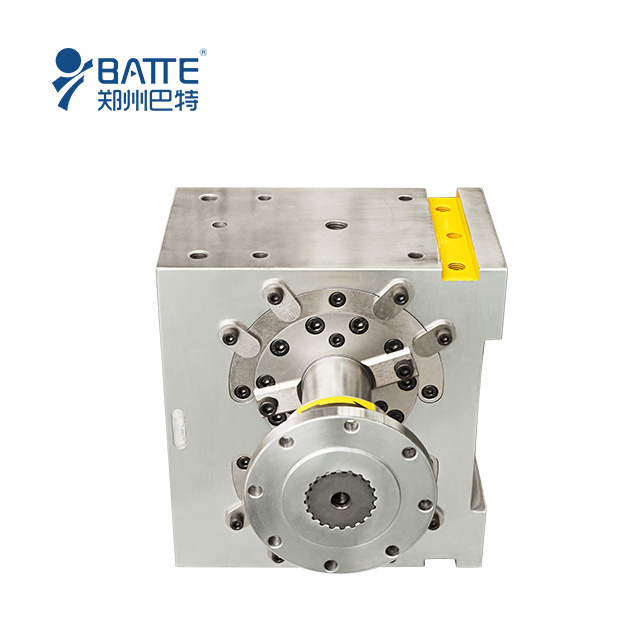
Rubber extruder melt pump has become the key equipment for the extrusion of rubber products, elastomers and compound materials through the stabilization of pressure and flow, self-cleaning and energy-saving features. Its application not only improves product quality and production efficiency, but also brings significant economic benefits to enterprises by reducing energy consumption and scrap rate.
Email: sale@meltpump.com
WhatsApp: +86 158 3833 1071